Test di invecchiamento accelerato
Test di invecchiamento UV
La luce ultravioletta della luce solare, poiché la sua energia luminosa è equivalente all’energia di legame dei legami chimici dei polimeri, può causare la rottura della catena del composto polimerico, che è il fattore principale che porta alla degradazione dei materiali polimerici.
Il test di invecchiamento ultravioletto si riferisce a un metodo di prova in cui i campioni di test di invecchiamento dei materiali polimerici vengono posizionati in un campo di luce ultravioletta ed esposti per ottenere il comportamento di invecchiamento e le leggi dei materiali polimerici.
In genere, il test di invecchiamento ultravioletto specificherà la regione ultravioletta e l’intensità della radiazione, come 40 W/m2, nell’intervallo di lunghezza d’onda di 300 nm-400 nm.
Le sorgenti luminose utilizzate nel test di invecchiamento UV di solito includono lampade allo xeno, lampade fluorescenti, lampade al trizio e lampade al deuterio. Tra queste, le lampade allo xeno possono simulare bene lo spettro solare e le lampade fluorescenti possono simulare bene lo spettro ultravioletto della luce solare.
Perché effettuare il test?
Ogni produttore desidera che il proprio prodotto resista quando viene utilizzato o conservato come previsto. Tuttavia, molte apparecchiature subiscono guasti dopo essere state sottoposte a forze atmosferiche per lunghi periodi di tempo. Mentre molte persone potrebbero pensare che l’acqua sia l’unico fattore ambientale che può influire negativamente su un pezzo di apparecchiatura metallica perché causa ruggine, non è così.
Anche il sole può avere un impatto significativo sulla qualità delle apparecchiature utilizzate all’esterno.
L’esposizione alla radiazione solare e al calore nel tempo può causare effetti indesiderati sulle proprietà visive e strutturali dei rivestimenti e dei materiali del substrato. Sia che siano esposti alla luce solare diretta o che la esplorino solo attraverso il vetro di una finestra (come l’interno di un’auto attraverso un parabrezza), i prodotti si degradano sotto la radiazione ultravioletta (UV) prodotta dal sole.
Accelerare il processo
Osservare e misurare i cambiamenti che i raggi UV possono produrre sarebbe un processo troppo lento in tempo reale. Per questo motivo, si eseguono test UV accelerati per simulare gli effetti dell’esposizione ambientale a lungo termine sui materiali campione.
Esponendo i campioni di prova alle radiazioni UV per periodi più lunghi e a livelli più intensi di quelli che incontrerebbero naturalmente, è possibile accelerare la simulazione per restituire i risultati di anni di esposizione effettiva in poche settimane.
Informazioni sul metodo
Il metodo prevede di posizionare il materiale campione in una camera UV fluorescente per sottoporlo a una quantità predeterminata di cicli. Questa macchina emette radiazioni UV a una intensità controllata per un dato periodo di tempo. Per simulare al meglio le condizioni reali, le nostre camere UV creano anche cicli meteorologici introducendo temperature, umidità e periodi di esposizione variabili.
Controllando tutti questi fattori meteorologici, i tecnici possono determinare meglio se il materiale campione resisterà per un periodo predeterminato in condizioni meteorologiche di utilizzo finale prevedibili.
Per qualsiasi altra informazione non esitate a contattarci
Scrivete la vostra richiesta qui sotto compreso i vostri recapiti e sarete contattati al più presto.
Oppure chiamate al numero:
+39 02 6707 2112
+39 02 6698 6366 R.A.
Oppure scrivete a :
Misuratori di brillantezza Gloss
Come si misura la brillantezza?
Un glossmetro (detto anche misuratore di lucentezza) è uno strumento utilizzato per misurare la riflessione speculare (lucentezza) di una superficie. La lucentezza è determinata proiettando un fascio di luce a intensità e angolo fissi su una superficie e misurando la quantità di luce riflessa a un angolo uguale ma opposto.
Sono disponibili diverse geometrie per la misurazione della lucentezza, ciascuna delle quali dipende dal tipo di superficie da misurare. Per i non metalli come rivestimenti e materie plastiche, la quantità di luce riflessa aumenta con l’aumento dell’angolo di illuminazione, poiché parte della luce penetra nel materiale della superficie e viene assorbita o diffusamente diffusa da esso a seconda del suo colore. I metalli hanno una riflessione molto più elevata e sono quindi meno dipendenti dall’angolazione.
Sono disponibili molti standard tecnici internazionali che definiscono il metodo di utilizzo e le specifiche per diversi tipi di glossmetro utilizzati su vari tipi di materiali, tra cui vernice, ceramica, carta, metalli e materie plastiche.
Molte industrie utilizzano i glossmetri nel loro controllo di qualità per misurare la lucentezza dei prodotti per garantire la coerenza nei loro processi di produzione.
L’industria automobilistica è uno dei principali utilizzatori del glossmetro, con applicazioni che spaziano dalla fabbrica all’officina di riparazione.
Scelta dell'angolo corretto per la misurazione della brillantezza
L’angolo di misurazione si riferisce all’angolo tra la luce incidente e quella riflessa. Sono specificati tre angoli di misurazione (20°, 60° e 85°) per coprire la maggior parte delle applicazioni di rivestimenti industriali. L’angolo viene selezionato in base all’intervallo di brillantezza previsto., come mostrato nella seguente tabella.
Ad esempio, se la misurazione effettuata a 60° è maggiore di 70 GU, l’angolo di misurazione dovrebbe essere modificato a 20° per ottimizzare la precisione della misurazione. Sono disponibili sul mercato due tipi di strumenti: strumenti ad angolo singolo a 60° e un tipo che combina 20°, 60° e 85°. Per altri materiali vengono utilizzati due angoli aggiuntivi. Un angolo di 45° è specificato per la misurazione di ceramiche, pellicole, tessuti e alluminio anodizzato, mentre 75° è specificato per la carta.
Taratura del glossmetro
Ogni glossmetro è impostato dal produttore per essere lineare in tutto il suo intervallo di misurazione calibrandolo su un set di piastrelle di calibrazione master riconducibili al NIST (National Institute of Standards and Technology).
Per mantenere le prestazioni e la linearità del glossmetro, si consiglia di utilizzare una piastrella standard di controllo. Questa piastrella standard ha valori di unità di lucentezza assegnati per ogni angolo di misurazione che sono anche riconducibili a standard nazionali come il NIST.
Lo strumento è calibrato su questo standard di controllo che è comunemente indicato come “piastrella di calibrazione” o “standard di calibrazione”.
L’intervallo di controllo di questa calibrazione dipende dalla frequenza di utilizzo e dalle condizioni operative del glossmetro. È stato visto che le piastrelle di calibrazione standard mantenute in condizioni ottimali possono contaminarsi e cambiare di alcune unità di lucentezza nel corso degli anni. Le piastrelle standard che vengono utilizzate in condizioni di lavoro richiederanno una calibrazione o un controllo regolari da parte del produttore dello strumento o dello specialista della taratura del glossmetro. Un periodo di un anno tra la ricalibrazione delle piastrelle standard dovrebbe essere considerato un periodo minimo.
Se uno standard di calibrazione si graffia o si danneggia in modo permanente in qualsiasi momento, richiederà una ricalibrazione o una sostituzione immediata, poiché il glossmetro potrebbe fornire letture errate. Gli standard internazionali stabiliscono che è la piastrella il manufatto calibrato e tracciabile, non il glossmetro, tuttavia i produttori spesso raccomandano di controllare anche lo strumento per verificarne il funzionamento a una frequenza dipendente dalle condizioni operative.
Applicazioni del misuratore di lucentezza
Il misuratore di lucentezza è utilizzato in molti settori, dalle cartiere all’automotive, e viene utilizzato sia dal produttore che dall’utente. Esempi includono:
- Vernici e rivestimenti
- Rivestimenti in polvere
- Additivi
- Inchiostri
- Materie plastiche
- Rivestimenti per legno, lucidanti e pavimenti
- Produzione di yacht
- Produzione e rifinitura di automobili
- Aerospaziale
- Pietra e metalli lucidati
- Elettronica di consumo
- Metalli anodizzati
Rivestimenti, lucidanti e pavimenti in legno
La lucentezza dei pavimenti in legno duro viene solitamente misurata a 60°. Le linee di finitura dei produttori di pavimenti in legno utilizzano da molti anni misuratori di lucentezza per misurare il livello di lucentezza nel controllo qualità (QC) per garantire di ottenere sempre una finitura visiva uniforme e quantificabile.
Per qualsiasi altra informazione non esitate a contattarci
Scrivete la vostra richiesta qui sotto compreso i vostri recapiti e sarete contattati al più presto.
Oppure chiamate al numero:
+39 02 6707 2112
+39 02 6698 6366 R.A.
Oppure scrivete a :
Misuratori di spessore
Uno spessimetro a ultrasuoni è particolarmente utile per la misurazione non distruttiva dello spessore quando l’accesso è possibile solo da un lato del materiale, ad esempio tubi o serbatoi. La misurazione dello spessore può essere eseguita sulla maggior parte dei materiali ingegneristici comuni, come metallo, plastica e vetro.
Misurazione non distruttiva dello spessore
Uno spessimetro a ultrasuoni è uno strumento fondamentale nei test non distruttivi (NDT), che funziona su principi simili al sonar ma a frequenze molto più elevate. Un trasmettitore emette un breve impulso di ultrasuoni nel materiale. Questo impulso si riflette sulla superficie opposta e ritorna a un ricevitore. Analizzando il tempo impiegato dall’impulso per tornare indietro, lo spessimetro calcola e visualizza lo spessore del materiale. Questo metodo consente una misurazione precisa dello spessore senza causare danni, rendendolo indispensabile in varie applicazioni industriali.
A cosa serve uno spessimetro?
Molti settori, come edilizia, costruzioni e produzione, hanno standard e normative rigorosi in merito allo spessore minimo consentito dei materiali per applicazioni specifiche. Gli spessimetri a ultrasuoni vengono utilizzati per misurare e verificare con precisione che gli spessori dei materiali soddisfino questi requisiti, garantendo un’adeguata protezione e qualità. Le misurazioni regolari dello spessore sono essenziali non solo per ispezionare le nuove fabbricazioni di apparecchiature, ma anche per monitorare gli elementi in servizio. Una misurazione coerente aiuta a prevedere i tassi di corrosione ed erosione, consentendo la valutazione della durata utile residua e la pianificazione proattiva della manutenzione.
Quanto è accurata la misurazione dello spessore a ultrasuoni?
Uno spessimetro misura lo spessore emettendo un impulso ultrasonico nel materiale e calcolando il tempo impiegato dall’eco per tornare dalla superficie opposta. Questa misurazione del tempo, combinata con la velocità nota del suono nel materiale, consente allo spessimetro di determinare lo spessore esatto.
La misurazione dello spessore a ultrasuoni è estremamente accurata, spesso fornendo una precisione entro pochi centesimi di millimetro. La precisione dipende dalla qualità dell’apparecchiatura, dalle proprietà del materiale testato e dall’esperienza dell’operatore. Una calibrazione corretta e un ambiente adatto possono aumentarne la precisione, rendendola una scelta affidabile per le applicazioni critiche.
Quali sono i vantaggi dell’utilizzo di spessimetri a ultrasuoni?
Gli spessimetri a ultrasuoni offrono diversi vantaggi:
• Non distruttivi: misurano lo spessore senza danneggiare il materiale, il che è perfetto per le ispezioni in corso
• Versatili: questi spessimetri possono essere utilizzati su un’ampia gamma di materiali, tra cui metalli, plastica, ceramica e compositi
• Efficienti: le misurazioni possono essere eseguite rapidamente e da un lato del materiale, il che è ideale per oggetti in aree difficili da raggiungere
• Sicuri: gli spessimetri a ultrasuoni sono sicuri da usare in quanto non emettono radiazioni nocive, a differenza di altri metodi di prova non distruttivi
Quale materiale non può essere utilizzato nei test di spessore a ultrasuoni?
I test di spessore a ultrasuoni in genere non sono adatti a materiali altamente porosi o con strutture a grana grossa, come alcuni tipi di legno o schiuma. Questi materiali possono disperdere le onde ultrasoniche, rendendo difficile ottenere letture accurate. Inoltre, anche i materiali privi di superfici parallele o estremamente sottili potrebbero presentare delle sfide per i test a ultrasuoni.
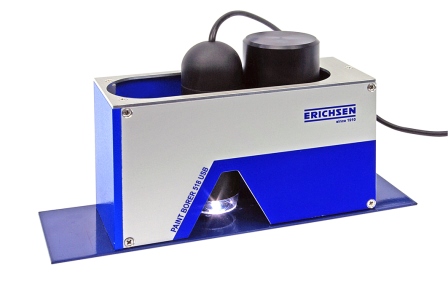
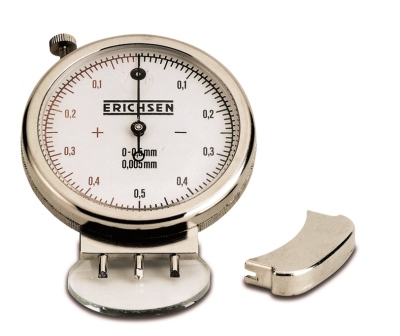
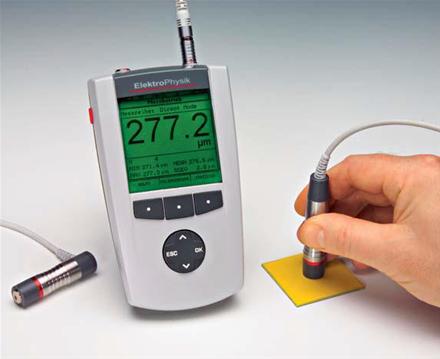
CO.FO.ME.GRA. SRL
Indirizzo : Via L. Zuccoli, 18 – 20125 Milano, Italy
Telefono :+39 02 6707 2112 – +39 02 6698 6366 R.A.
E-mail: info@cofomegra.it
Metodi di prova per l'adesione del rivestimento
Per far sì che i rivestimenti funzionino in modo soddisfacente, devono aderire ai substrati su cui vengono applicati. Per determinare quanto bene un rivestimento è legato al substrato, si possono usare vari metodi riconosciuti.
Le tecniche di misurazione comunemente utilizzate sono eseguite con un coltello o con un tester di adesione pull-off. Dopo qualsiasi test è importante registrare se il cedimento del legame è stato adesivo (cedimento all’interfaccia rivestimento/substrato), coesivo (cedimento all’interno della pellicola di rivestimento o del substrato) o cedimento della colla (separazione visibile della colla da se stessa). Molti standard nazionali e internazionali richiedono che venga registrata la natura della frattura.
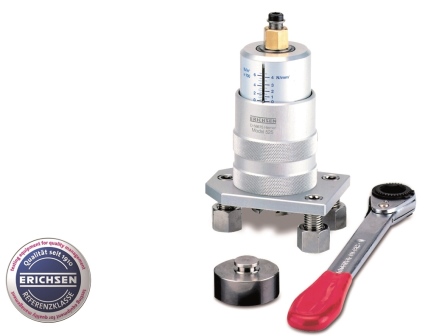
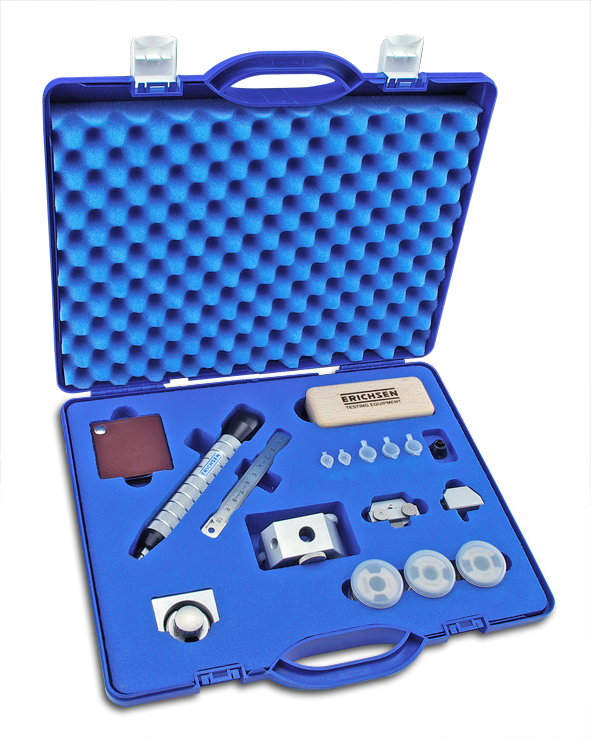
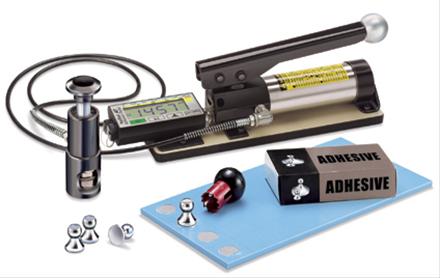
Cos’è un test del coltello?
Questo semplice test richiede l’uso di un taglierino per prendere il rivestimento. Stabilisce se l’adesione di un rivestimento a un substrato o a un altro rivestimento (in sistemi multistrato) è a un livello generalmente adeguato. Le prestazioni si basano sia sul grado di difficoltà di rimozione del rivestimento dal substrato sia sulle dimensioni del rivestimento rimosso.
Utilizzando il coltello e la guida di taglio, viene eseguito un taglio a X attraverso il rivestimento fino al substrato. Al vertice, la punta del coltello viene utilizzata per tentare di sollevare il rivestimento dal substrato o dal rivestimento sottostante.
Questo è un test altamente soggettivo e il suo valore dipende dall’esperienza dell’ispettore. Un rivestimento che ha un alto grado di resistenza coesiva può sembrare avere un’adesione peggiore di uno che è fragile e quindi si frattura facilmente quando viene sondato. Non esiste alcuna correlazione nota con altri metodi di test di adesione (test di adesione a strappo, nastro adesivo, ecc.).
Un metodo standard per l’applicazione e l’esecuzione di questo test è disponibile in ASTM D6677—Metodo di prova standard per la valutazione dell’adesione mediante coltello.
Cos’è un test del nastro?
Su substrati metallici, una versione più formale del test del coltello è il test del nastro. Il nastro sensibile alla pressione viene applicato e rimosso sui tagli fatti nel rivestimento. Esistono due varianti di questo test: il test del nastro con taglio a X e il test del nastro con tratteggio incrociato.
Il test del nastro con taglio a X è principalmente destinato all’uso nei cantieri. Utilizzando una lametta affilata, un bisturi, un coltello o un altro dispositivo di taglio, viene eseguito un taglio a X attraverso il rivestimento fino al substrato. Viene utilizzato un righello in acciaio o altro metallo duro per garantire tagli dritti. Il nastro viene posizionato al centro dell’intersezione dei tagli e quindi rimosso rapidamente. L’area del taglio a X viene quindi ispezionata per la rimozione del rivestimento dal substrato o dal rivestimento sottostante e valutata.
Il test del nastro a tratteggio incrociato è principalmente destinato all’uso in laboratorio su rivestimenti di spessore inferiore a 5 mils (125 micron). Utilizza un motivo a tratteggio incrociato anziché un motivo a X. È necessaria una guida di taglio o una speciale taglierina a tratteggio incrociato con più lame preimpostate per assicurarsi che le incisioni siano opportunamente distanziate e parallele. Dopo che il nastro è stato applicato e rimosso, l’area di taglio viene quindi ispezionata e valutata.
Un metodo standard per l’applicazione e l’esecuzione di questi test è disponibile in ASTM D3359—Standard Test Methods for Rating Adhesion by Tape Test.
Cos’è un test di adesione pull-off?
Un test più quantitativo per l’adesione è il test pull-off in cui un dispositivo di carico, comunemente chiamato dolly o stub, viene fissato tramite un adesivo a un rivestimento. Utilizzando un tester di adesione pull-off portatile, come il PosiTest AT, viene applicato un carico crescente fino a quando il dolly non viene staccato. La forza richiesta per staccare il dolly o la forza che il dolly ha sopportato, produce la resistenza alla trazione in libbre per pollice quadrato (psi) o mega Pascal (MPa). La rottura si verificherà lungo il piano più debole all’interno del sistema composto da dolly, adesivo, sistema di rivestimento e substrato e sarà esposta dalla superficie di frattura.
Questo metodo di prova massimizza la sollecitazione di trazione rispetto alla sollecitazione di taglio applicata da altri metodi, come l’adesione a raschiamento o a coltello, e i risultati potrebbero non essere confrontabili. Inoltre, le misurazioni della resistenza al pull-off dipendono dallo strumento utilizzato nel test. I risultati ottenuti utilizzando dispositivi diversi o risultati per gli stessi rivestimenti su substrati con diversa rigidità potrebbero non essere confrontabili.
I tester di adesione pull-off portatili funzionano utilizzando la pressione meccanica (torsione manuale), idraulica (olio) o pneumatica (aria). Sono classificati come allineati fissi o autoallineanti a seconda della loro capacità di garantire una forza di pull-off verticale. La migliore ripetibilità si ottiene quando la forza di pull-off agisce perpendicolarmente alla superficie sottoposta a test.
La disponibilità di una gamma completa di modelli di tester di adesione pull-off facilita la misurazione dell’adesione del rivestimento su quasi tutti i substrati rigidi. Ad esempio, i dolly da 20 mm possono essere ideali per le tipiche resistenze di adesione del rivestimento su metallo, plastica e legno, mentre i dolly da 50 mm sono più ideali per rivestimenti con resistenze di adesione inferiori su substrati in muratura come il calcestruzzo. È possibile utilizzare diverse dimensioni di dolly per soddisfare esigenze di misurazione speciali.
Ad esempio, riducendo le dimensioni del dolly da 20 mm a 10 mm, aumenta l’intervallo di pull-off del calibro di 4 volte, consentendo ad alcuni produttori di misurare con precisione le resistenze di adesione oltre 12.000 psi (82 MPa). I dolly economici eliminano la necessità di riutilizzo, semplificando notevolmente il processo di preparazione, con un ulteriore vantaggio di consentire la conservazione di campioni fisici per riferimento futuro o prova dei risultati del test di pull-off.
Il tester di adesione PosiTest AT è la soluzione DeFelsko per eseguire con precisione un test di adesione del rivestimento. Disponibile sia nei modelli Manual (PosiTest AT-M) che Automatic (PosiTest AT-A), il tester di adesione pull-off misura l’adesione dei rivestimenti a metallo, legno, cemento e altri substrati rigidi. Fai clic qui per saperne di più sul PosiTest AT.
Cos’è un test di raschiatura?
Un test di raschiatura viene in genere eseguito in laboratorio ed è limitato ai test su superfici di pannelli lisci e piatti. L’adesione viene determinata spingendo i pannelli rivestiti sotto uno stilo arrotondato o un anello che viene caricato in quantità crescenti fino a quando il rivestimento non viene rimosso dalla superficie del substrato. Viene utilizzato un dispositivo chiamato tester di raschiatura-adesione a trave bilanciata.
Un metodo standard per l’applicazione e l’esecuzione di questo test è disponibile in ASTM D2197—Metodo di prova standard per l’adesione di rivestimenti organici mediante adesione a raschiatura.
Altri metodi di test di adesione
Esistono molti altri test di adesione. Alcuni di questi comportano l’uso di macchine per prove di trazione con vernice applicata al substrato con una striscia di tessuto incorporata nella vernice (la macchina per prove di trazione tira il substrato e il tessuto) o hanno la vernice applicata tra due fogli del substrato (la macchina per prove di trazione tira entrambi i pezzi del substrato). ASTM D2370 descrive uno di questi test di allungamento, resistenza alla trazione e rigidità di pellicole organiche quando testate come pellicole libere. L’adesione del rivestimento organico ai substrati di plastica mediante il montaggio di un perno di alluminio e la sua rimozione con un tester di trazione è trattata in ASTM D5179.
ASTM D4145 descrive un test di flessione per determinare la flessibilità e l’adesione dei rivestimenti su substrati metallici preverniciati. Questi rivestimenti organici sono sottoposti a sollecitazioni quando vengono fabbricati in prodotti mediante profilatura a rulli, piegatura a freno o altri processi di deformazione. Queste sollecitazioni possono superare la flessibilità o la forza adesiva del rivestimento, con conseguente frattura del rivestimento, esposizione del substrato o perdita di aderenza al substrato. Questo test è un mezzo per valutare la capacità di un sistema di rivestimento di resistere alle sollecitazioni di fabbricazione.
I test di formabilità e adesione di rivestimenti complessi di primer/cromato ricchi di zinco applicati in fabbrica su acciaio sono descritti in ASTM 4146. In questo test, un campione rivestito viene allungato biassialmente per una determinata distanza in una macchina appropriata, viene applicato del nastro adesivo all’area deformata (cupola) e poi tirato via, e la quantità di rivestimento rimossa viene confrontata con uno standard fotografico per determinare il grado di adesione del rivestimento.
L’adesione è anche un risultato misurabile di alcuni test di durezza effettuati tramite durezza a matita, gravelometro, impatto (freccia cadente, ecc.) o piegatura del mandrino. Durante questi test si dovrebbe registrare la scheggiatura del rivestimento. Infine, si può notare la perdita di aderenza durante alcuni test di resistenza chimica in cui il rivestimento forma bolle, bolle o addirittura cade.
Contatti
CO.FO.ME.GRA. SRL
Indirizzo : Via L. Zuccoli, 18 – 20125 Milano, Italy
Telefono :+39 02 6707 2112 – +39 02 6698 6366 R.A.
E-mail: info@cofomegra.it
Misura della viscosità
Cos’è la viscosità e perché è importante misurarla?
La viscosità è una proprietà ampiamente misurata ed è fondamentale in una vasta gamma di settori e prodotti. Le proprietà reologiche di un fluido sono importanti per molte ragioni.
• Il prodotto avrà lo stesso aspetto e la stessa sensazione che il mio cliente si aspetta? Ad esempio, se un gel doccia è troppo liquido, quando il cliente cerca di applicarlo, si dissiperà e dovrà usare più prodotto per potersi lavare. Al contrario, se è troppo denso, non ne userà abbastanza e sarà anche molto difficile estrarlo dalla bottiglia.
• La viscosità del fluido è fondamentale quando viene pompato attraverso una tubazione o un sistema di dosaggio; se la viscosità è troppo alta, la pompa non sarà in grado di farcela.
• La quantità di prodotto erogata in un processo, sia automatico che manuale, è influenzata dalle sue proprietà reologiche.
• Nella stampa, la viscosità dell’inchiostro ha enormi effetti sulla qualità di stampa.
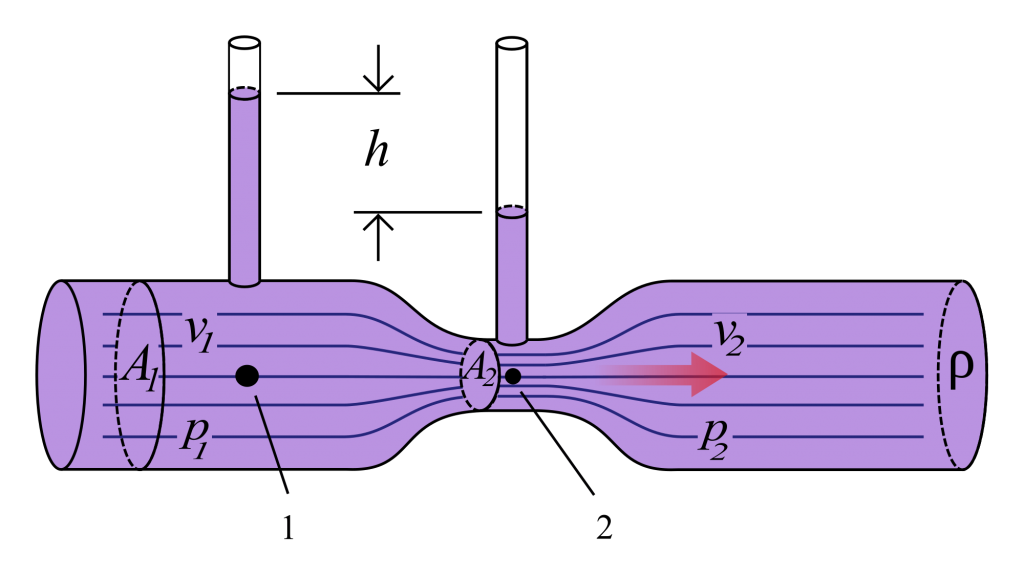
Fluidi newtoniani
I fluidi newtoniani prendono il nome da Sir Isaac Newton. Egli descrisse i comportamenti di flusso dei fluidi con una relazione lineare tra sforzo di taglio [mPa] e velocità di taglio [1/s]. Questa relazione è nota come legge di viscosità di Newton, in cui la costante di proporzionalità η è la viscosità [mPa-s] del fluido: Alcuni esempi di fluidi newtoniani: acqua, miele, alcol, olio per questi liquidi solo la temperatura influenza la viscosità.
Fluidi non newtoniani
Fluidi non newtoniani, quindi la loro viscosità dipende dalla velocità di taglio (Shear Thinning o Thickening) o dalla storia di deformazione (fluidi tissotropici). I fluidi non newtoniani mostrano una relazione non lineare tra sforzo di taglio e velocità di taglio, hanno uno sforzo di snervamento o una viscosità che dipende dal tempo o dalla storia di deformazione o da una combinazione di tutto quanto sopra. Alcuni esempi di fluidi non newtoniani: amido di mais e acqua, ketchup, adesivi, creme sia la velocità del fuso che la temperatura influenzano la viscosità.
Viscosità dinamica
La viscosità dinamica è la misura della resistenza di un fluido al flusso di taglio quando viene applicata una forza esterna. È utile per descrivere il comportamento dei fluidi sotto stress. Principalmente, è molto utile per descrivere i fluidi non newtoniani osservando come la viscosità cambia al variare della velocità di taglio.
Come si misura la viscosità?
Esistono due tipi principali di viscosimetro e metodi di classificazione delle proprietà reologiche del liquido. I tipi principali sono elencati di seguito; All’interno di questi tipi, ci sono molti sottotipi e metodi.
Viscosimetri capillari in vetro e tazze di flusso
Questi sono gli strumenti più semplici per la misurazione della viscosità. Un volume di liquido impostato viene fatto passare attraverso un orifizio di dimensioni note, il tempo impiegato per questo liquido viene misurato e (tempo di efflusso) viene quindi calcolato in un’unità di misura della viscosità cinematica come centistokes (cSt). I viscosimetri capillari in vetro e le tazze di flusso sono disponibili in molti tipi, tutti realizzati secondo standard diversi. Viscosimetro rotazionale
I viscosimetri rotazionali funzionano misurando la coppia creata dall’albero e dal mandrino. Come i viscosimetri capillari, ci sono diversi tipi di viscosimetro rotazionale con molte diverse dimensioni e forme del mandrino adatte a quasi tutte le misurazioni della viscosità del fluido. In AML, offriamo un’ampia gamma di servizi di riparazione della calibrazione della viscosità e apparecchiature per test della viscosità, tra cui Melt Flox Index e Flow Cups.
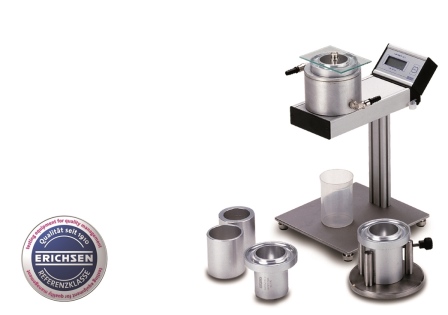
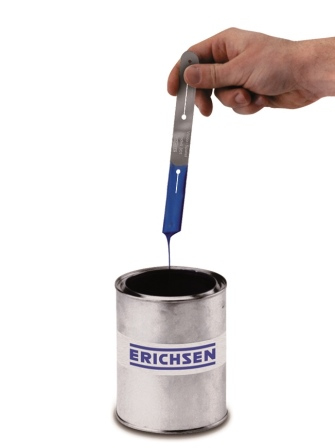
CO.FO.ME.GRA. SRL
Indirizzo : Via L. Zuccoli, 18 – 20125 Milano, Italy
Telefono :+39 02 6707 2112 – +39 02 6698 6366 R.A.
E-mail: info@cofomegra.it
Test durezza rivestimenti
La durezza di un materiale di rivestimento è una proprietà relativa che può essere interpretata in vari modi da diversi settori che utilizzano materiali di rivestimento/rivestimento. Mentre i test di durezza vengono spesso utilizzati per valutare il grado di polimerizzazione, possono anche essere utilizzati per misurare le proprietà di durezza formulate nei rivestimenti.
La durezza assoluta di un rivestimento non è sempre l’obiettivo finale della formulazione e un aumento della durezza può essere accompagnato da fragilità o da una diminuzione della flessibilità del rivestimento. L’equilibrio della durezza con altre proprietà finali del film è determinato dall’uso finale del prodotto.
Quando si confrontano i valori di durezza elencati nella scheda tecnica di un produttore di rivestimenti, le informazioni sono spesso considerate un’indicazione del suo grado di polimerizzazione e delle sue caratteristiche prestazionali intrinseche.
Un rivestimento non polimerizzato che rimane morbido può subire danni durante il servizio; ad esempio, riempiendo un fosso troppo rapidamente e danneggiando un rivestimento per tubi appena applicato che non ha raggiunto la sua completa polimerizzazione, il che può avere un impatto negativo sull’integrità della conduttura.
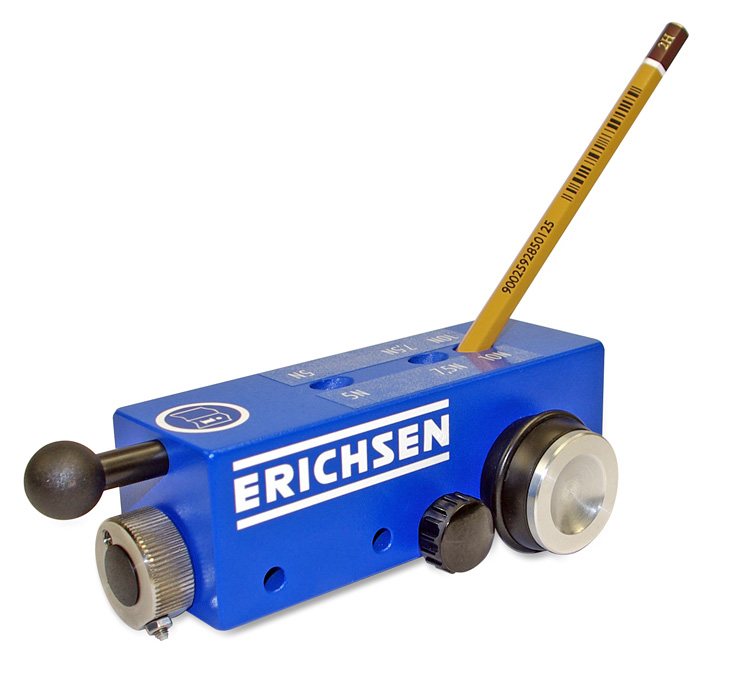
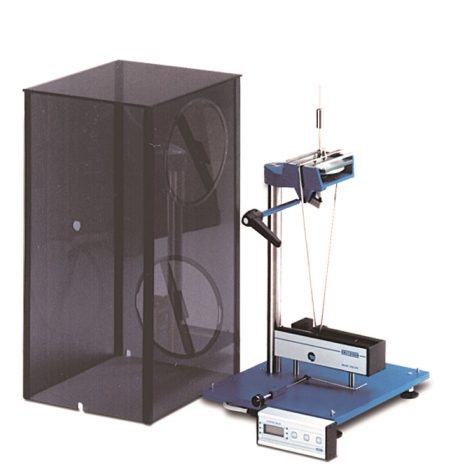
In questo articolo sono descritti due metodi di prova comuni: il tester di tipo indentatore (Durometro) e la durezza a matita, che è più un test di durezza a taglio. La selezione del metodo di prova è spesso dettata dallo spessore dei materiali di rivestimento, sebbene siano consentite variazioni negli spessori testati se è possibile ottenere informazioni utili.
La durezza dei rivestimenti a film spesso (il metodo indica che “film spesso” è considerato un minimo di 6 mm o 240 mils) è in genere misurata utilizzando un tester di tipo indentatore che misura la resistenza all’indentazione sotto un carico di forza della molla specifico, mentre i rivestimenti a film sottile (un riferimento allo spessore non è incluso nel metodo) sono spesso valutati per il grado di durezza utilizzando il test di durezza a matita.
Si noti che non vi è alcuna correlazione tra i metodi di prova di durezza descritti nel presente documento e non vi è alcun criterio di superamento/fallimento indicato nei rispettivi metodi di prova standard ASTM. Le specifiche del progetto dovrebbero indicare il valore di durezza minimo accettabile prima di mettere in servizio il sistema di rivestimento. Il valore di durezza minimo accettabile è spesso stabilito dal produttore del rivestimento.
Misurazione della durezza col durometro
Il test di durezza con durometro viene eseguito secondo la procedura descritta in ASTM D2240, Metodo di prova standard per le proprietà della gomma – Durezza con durometro. Questo standard copre dodici tipi di dispositivi di misurazione (tipi A, B, C, D, DO, O, OO, OOO, OOO-S e R).
Questo articolo descrive l’uso di un durometro Shore D, poiché molti dei rivestimenti a film spesso e resistenti alle sostanze chimiche rientrano nell’intervallo di durezza che un durometro Shore D può misurare con precisione.
Per materiali di rivestimento a film spesso e più morbidi, un durometro Shore A può essere più utile poiché ha una forza elastica inferiore. Secondo lo standard ASTM, i valori di durezza con durometro inferiori a 20 e superiori a 90 non sono considerati affidabili e suggerisce di non registrare letture inferiori a 20 e superiori a 90 per gli strumenti Shore A o Shore D.
Contatti
CO.FO.ME.GRA. SRL
Indirizzo : Via L. Zuccoli, 18 – 20125 Milano, Italy
Telefono :+39 02 6707 2112 – +39 02 6698 6366 R.A.
E-mail: info@cofomegra.it
Imbutitura Metalli
L’imbutitura profonda è un processo di produzione ampiamente utilizzato nella formatura di lamiere in strutture simili a tazze o scatole. Pentole e padelle per cucinare, recipienti, lavelli, parti di automobili, come pannelli e serbatoi di gas, sono solo alcuni degli articoli prodotti con l’imbutitura della lamiera.
Questo processo è talvolta chiamato disegno e non deve essere confuso con il processo di deformazione di massa del disegno discusso in precedenza. Un’operazione di imbutitura profonda di base potrebbe essere la formatura di un foglio piatto in una tazza tridimensionale o una scatola. La forma di una parte imbutita non è limitata a un cerchio o quadrato, sono possibili contorni più complessi.
Tuttavia, con l’aumentare della complessità, le difficoltà di fabbricazione aumentano rapidamente. È meglio progettare la forma di un disegno profondo per essere il più semplice possibile. Per il processo di imbutitura profonda della lamiera primaria, la parte avrà una base piatta e lati diritti.
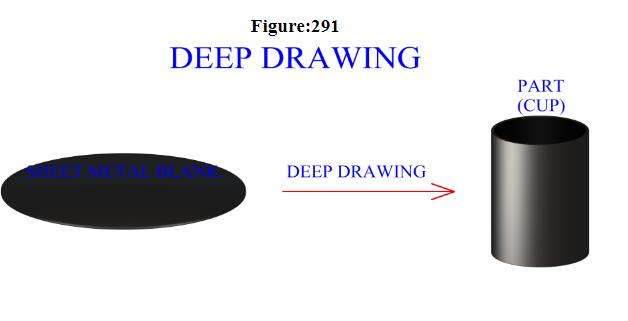
Il processo
L’imbutitura profonda della lamiera viene eseguita con punzone e matrice. Il punzone è la forma desiderata della base del pezzo, una volta disegnato. La cavità della matrice combacia con il punzone ed è un po’ più ampia per consentirne il passaggio e il gioco. Questa impostazione è simile alle operazioni di taglio della lamiera. Come nel taglio, il gioco è la distanza laterale tra il bordo della matrice e il bordo del punzone. Il pezzo in lamiera, chiamato pezzo grezzo, viene posizionato sopra l’apertura dello stampo. Un premilamiera, che circonda il punzone, esercita una pressione sull’intera superficie del grezzo (eccetto l’area sotto il punzone), tenendo la lamiera in piano contro lo stampo. Il pugno viaggia verso il grezzo. Dopo aver toccato il pezzo, il punzone forza la lamiera nella cavità dello stampo, formandone la forma.
Le attrezzature per l’imbutitura della lamiera implicherebbero una doppia azione, una per il premilamiera e una per il punzone. Sia le presse meccaniche che quelle idrauliche sono utilizzate nell’industria manifatturiera. Tipicamente la pressa idraulica può controllare separatamente le azioni del premilamiera e del punzone, ma la pressa meccanica è più veloce. I materiali per punzoni e matrici, per l’imbutitura profonda della lamiera, sono generalmente acciai per utensili e ferro.
Tuttavia, la gamma di materiali per punzoni e matrici può spaziare dalla plastica ai metalli duri. Le parti vengono solitamente disegnate a velocità comprese tra 4 e 12 pollici al secondo.
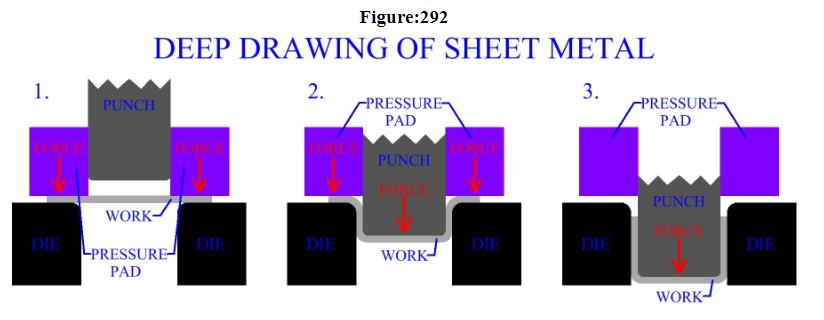
Pratica di imbutitura profonda
L’imbutitura è un processo di formatura della lamiera che comporta un flusso di materiale complesso e distribuzioni di forza. Come accennato, l’impostazione del punzone e dello stampo è in qualche modo simile a un’operazione di taglio della lamiera, come la punzonatura o la tranciatura. Due fattori principali faranno sì che il punzone nell’imbutitura profonda attiri il metallo nella cavità dello stampo, piuttosto che tagliarlo.
Un fattore importante nello stampaggio profondo è il raggio dell’angolo dello stampo e il raggio dell’angolo del punzone. Quando si taglia la lamiera, i bordi del punzone e della matrice non hanno un raggio. Gli spigoli vivi del punzone e della matrice ne provocano il taglio. Un raggio su un bordo cambierà la distribuzione della forza e farà scorrere il metallo sopra il raggio e nella cavità dello stampo. L’altro fattore principale che fa sì che il punzone imbutisca la lamiera e non la tagli, è la quantità di gioco. Il gioco nelle operazioni di taglio è relativamente piccolo, solitamente dal 3% all’8% dello spessore della lamiera. Nella produzione di imbutitura profonda, se il gioco è troppo piccolo, la lamiera può essere tagliata o perforata (non bene), nonostante il raggio. Il gioco nella produzione di imbutitura profonda è maggiore dello spessore della lamiera, solitamente i valori di gioco vanno dal 107% al 115% dello spessore della lamiera.
Per molti calcoli si presume che lo spessore della lamiera rimanga costante. Tuttavia, ci sono cambiamenti di spessore in alcune aree, a causa delle forze in gioco. Per formare le pareti laterali del pezzo, il materiale deve fluire dalla periferia del grezzo sopra il raggio dell’angolo dello stampo, quindi dritto nella direzione del punzone. Il materiale che forma la parete diritta è sottoposto a sollecitazione di trazione che ne causerà naturalmente l’assottigliamento.
I fattori del processo di imbutitura profonda sono controllati per mitigare l’assottigliamento, ma un certo assottigliamento della lamiera è inevitabile. L’assottigliamento massimo si verificherà molto probabilmente sulla parete laterale, vicino alla base della parte. Una parte disegnata correttamente può presentare una riduzione dello spessore fino al 25% in alcune aree.
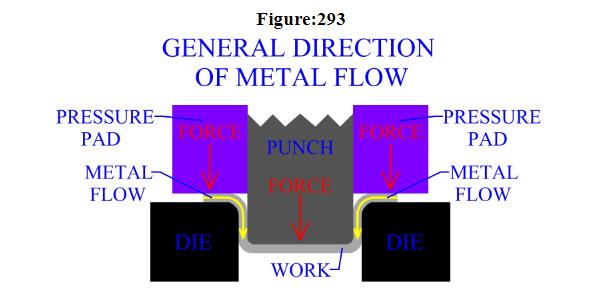
Rapporto di disegno
È possibile quantificare la misurazione della quantità di imbutitura eseguita su uno sbozzato di lamiera. Questo può essere fatto con il rapporto di disegno. Maggiore è il rapporto di imbutitura, più estrema è la quantità di imbutitura profonda. A causa della geometria, delle forze, del flusso del metallo e delle proprietà del materiale del lavoro, esiste un limite alla quantità di imbutitura profonda che può essere eseguita su una lamiera grezza in un’unica operazione. I rapporti di imbutitura possono aiutare a determinare la quantità massima di imbutitura possibile. Il rapporto di disegno è approssimativamente calcolato come,
DR = Db/Dp.
Db è il diametro del grezzo e Dp è il diametro del punzone. Per le forme non circolari a volte viene utilizzato il diametro massimo o occasionalmente il rapporto di disegno viene calcolato utilizzando le aree superficiali. Il limite al rapporto di disegno per un’operazione è solitamente 2 o inferiore. I limiti effettivi alla quantità di imbutitura possibile dipendono anche dalla profondità dell’imbutitura, dal raggio del punzone, dal raggio della matrice, dall’anisotropia del foglio e dal materiale del pezzo grezzo.
Riduzione
Un altro modo per esprimere il rapporto di disegno è la riduzione (r). La riduzione viene misurata utilizzando le stesse variabili del rapporto di stiro. La riduzione può essere calcolata con r = (Db – Dp)/(Db).
Db e Dp sono rispettivamente i diametri del grezzo e del punzone. La riduzione dovrebbe essere 0,5 o meno. Spesso espressa come riduzione percentuale r = (Db – Dp)/(Db) X 100%. In questo caso la riduzione dovrebbe essere pari o inferiore al 50%.
Ridisegno lamiera
Se la riduzione percentuale richiesta della lamiera è superiore al 50%, la parte deve essere formata in più operazioni. Il ridisegno è il successivo disegno profondo di un’opera che ha già subito un processo di disegno profondo. Utilizzando più di un’operazione, è possibile ottenere una maggiore ampiezza di imbutitura profonda.
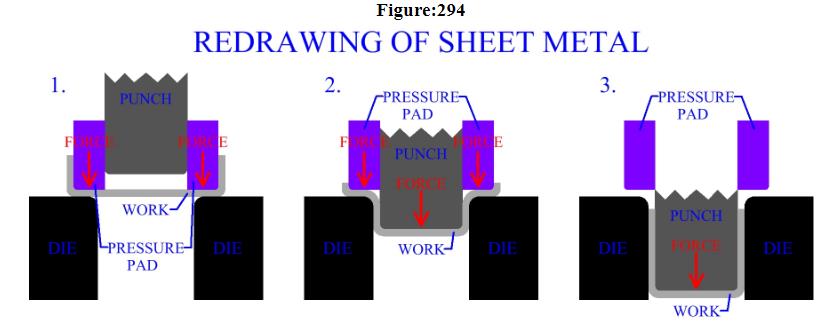
La quantità di formatura della lamiera che può essere realizzata al primo ridisegno è inferiore rispetto al disegno originale. Per il disegno originale del pezzo grezzo la riduzione del 50% è usata raramente durante la pratica di produzione industriale.
La riduzione iniziale è solitamente dal 35% al 45%. Il primo ridisegno viene comunemente eseguito con una riduzione dal 20% al 30%. Il secondo ridisegno può in genere variare dal 13% al 16% di riduzione. Se deve essere eseguita una notevole quantità di imbutitura profonda e sono necessarie diverse operazioni di ridisegno, la parte deve essere ricotta ogni due operazioni. Questo recupererà il materiale per ulteriori ridisegni.
La progettazione del processo di imbutitura profonda deve includere il disegno di forme di parti intermedie, in situazioni che richiedono il ridisegno. Per ogni ridisegno da eseguire ci sarà una parte intermedia.
CO.FO.ME.GRA. SRL
Indirizzo : Via L. Zuccoli, 18 – 20125 Milano, Italy
Telefono :+39 02 6707 2112 – +39 02 6698 6366 R.A.
E-mail: info@cofomegra.it
Camere a nebbia salina
Il test in nebbia salina, noto anche come test in nebbia salina, è una valutazione standardizzata della resistenza alla corrosione dei materiali metallici, con o senza rivestimento, temporaneo o permanente, per la protezione contro la corrosione.
La conduzione di questi test è descritta da vari standard ( ASTM B117, DIN 50021, EN ISO 9227). In tutti i casi, le parti da valutare vengono poste in una camera di prova in cui viene vaporizzata una soluzione salina ad una certa temperatura. Il test può essere eseguito ininterrottamente da sei a più di mille ore. I materiali più resistenti alla corrosione possono essere testati più a lungo.
Il test in nebbia salina darà risultati diversi dalla corrosione in condizioni normali. La corrosione è davvero un fenomeno complesso. Tuttavia, il test in nebbia salina è un metodo di controllo della qualità del rivestimento ampiamente utilizzato nell’industria.

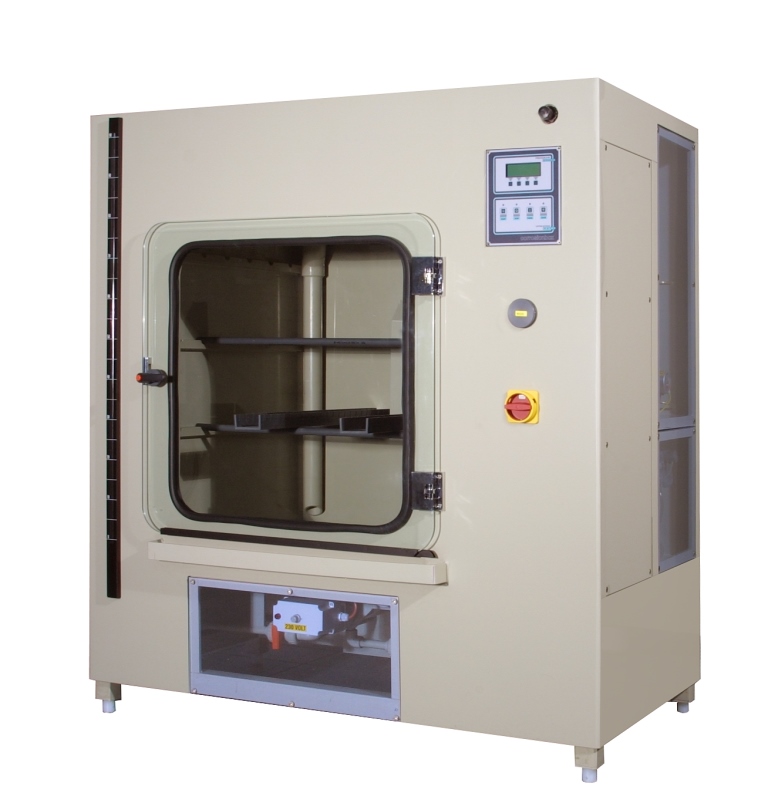
Nella camera di prova, la vaporizzazione di una soluzione salina produce un’atmosfera favorevole alla corrosione che attacca la parte in prova. In queste condizioni il fenomeno di corrosione viene accelerato e i rivestimenti perdono le loro proprietà protettive. La durata del test dipenderà dalla qualità del rivestimento. Impostando i parametri di concentrazione della soluzione salina, temperatura, pressione e pH, i risultati sono riproducibili
Tipi di test
Distinguiamo, a seconda della soluzione utilizzata:
test in nebbia salina neutra utilizzando una soluzione di cloruro di sodio (NaCl) a pH neutro: test NSS ( Neutral Salt Spray );
test in nebbia salina acetica con aggiunta di acido acetico alla soluzione salina: ASS test ( Acetic Acid Salt Spray );
Nebbia salina cupro-acetica accelerata test con l’aggiunta di rame (II) cloruro alla soluzione salina: prova CASS ( rame Accelerated test della nebbia salina ).
I test ASS e CASS sono particolarmente indicati per rivestimenti galvanici decorativi come rivestimenti Cu-Ni-Cr o Ni-Cr, ma anche per rivestimenti anodici di alluminio.
Attrezzature
La camera di prova ha un volume minimo di quattrocento litri che sarà adattato alle dimensioni delle parti da testare. Il telaio e l’interno della camera saranno realizzati in materiale inerte alla corrosione per evitare qualsiasi reazione di corrosione tra i campioni da testare e la camera.
A seconda delle sue dimensioni, la camera sarà dotata di uno o più ugelli per la nebulizzazione della soluzione.
La pressione dell’aria sarà regolabile per consentire una buona distribuzione della nebbia durante l’irrigazione. Inoltre, l’apparecchiatura avrà un serbatoio contenente la soluzione da irrorare. Un sistema di riscaldamento controllerà la temperatura della camera durante il test.
Una camera utilizzata per i test ASS o CASS è difficile da pulire. Per questo motivo a tali prove sarà dedicata una camera per i test NSS.
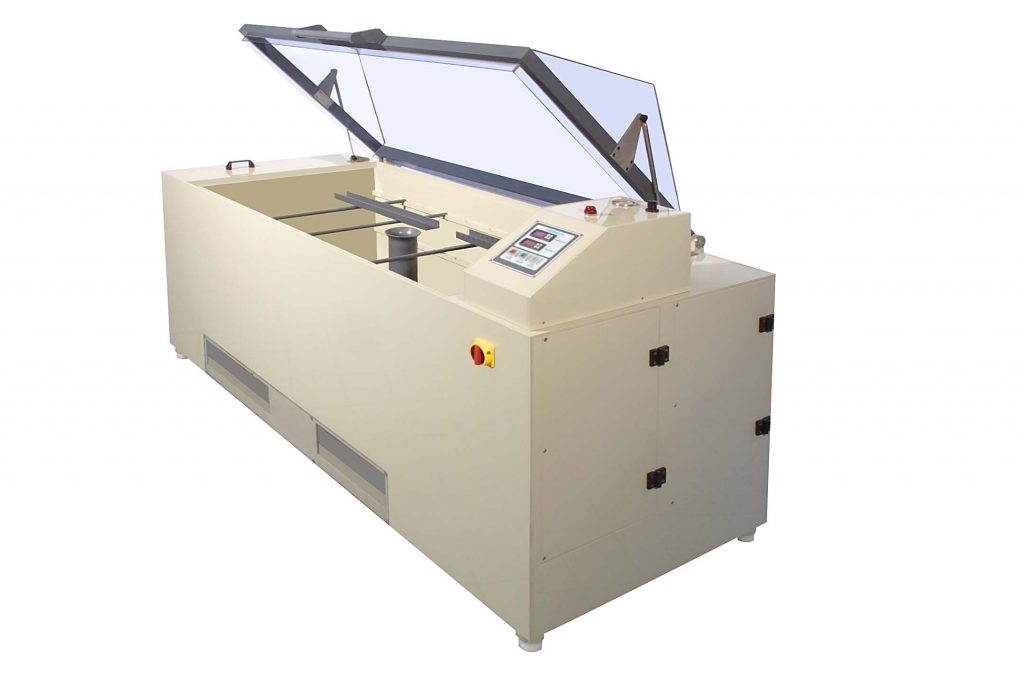
Standard
Gli standard internazionali come ASTM B117 o EN ISO 9227 definiscono la procedura per il test senza descrivere un metodo per valutare le superfici corrose o indicare la durata del test. La valutazione dei prodotti corrosi dovrà quindi essere fissata tra i protagonisti.
Per i prodotti verniciati, lo standard ISO4628-3 descrive i livelli di ruggine in sei categorie da Ri0 (assenza di ruggine) a Ri5 (dal 4 al 50% della superficie arrugginita). Il livello Ri1 (0,05%) dopo un test in nebbia salina è un massimo spesso adottato.
Lo standard IEC 60068-2-11 descrive anche un test in nebbia salina. Fa parte di una serie di standard relativi alle condizioni ambientali.
Nell’industria automobilistica, gli standard definiscono i criteri per valutare la qualità delle superfici. Un acciaio protetto presenta ruggine rossa (ossido di ferro) una volta che il rivestimento non offre più una protezione sufficiente. Uno strato di zinco mostrerà ruggine bianca ( ossido di zinco ) dopo solo poche ore nella camera. La corrosione si manifesterà sotto forma di punti bianchi che alla fine si trasformeranno in punti rossi, segno della corrosione dell’acciaio. Per rafforzare le proprietà protettive dello zinco e aumentare il tempo prima che compaia la ruggine bianca, è possibile utilizzare la passivazione, la cromatura, la verniciatura a polvere, ecc.
Un rivestimento protettivo deve fornire una durata minima senza corrosione.